SECONDARY PROCESSES
AT NEWBEC

PHOSPHATING
-
Phosphating (or phosphatizing) is a surface treatment used on steels to prevent corrosion, enhance the surface for other protective coatings, or for lubricity.
-
It is formed by creating a layer of crystal salts of iron and zinc or iron and manganese in a phosphoric acid solution. At Newbec, we create the protective layer using zinc.
-
Most common uses of phosphating are related to carbon steels, cast iron or to high and low strength alloy carbon steels.
-
Phosphatizing can be achieved by immersing the part into a bath or by spraying the part with the phosphating solution. A chemical reaction takes place that causes the zinc (or manganese) phosphate salts to adhere to the part surface.
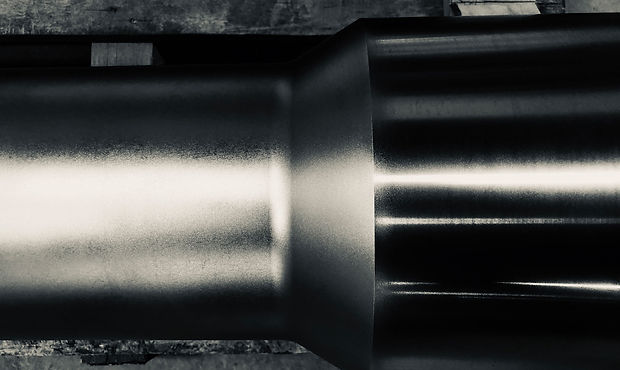
SHOT PEENING
-
Shot peening is a mechanical process used to create a compressive residual stress layer on the surface of a metal part to enhance its mechanical properties, especially fatigue resistance.
-
The metal surface is modified by striking it with high velocity particles (shots) that plastically deform (compress) the metal surface.
-
The shots are usually metal pellets from certain specific sizes and hardness. Selection of the pellets depends on the compressive stress to be induced. The higher the shot size, the higher the compressive layer induced.
-
Shot peening is desired in areas that are subject to high stress concentration where microcracks can potentially be formed, such as thread connections. Microcracks do not generate or propagate in areas under compressive stress.
-
Newbec has the trained and certified personnel to ensure the process is done correctly.
-
Shot peening material is usually referred to as “shot media.”
-
Most common type of shot media used in the oil and gas industry are:
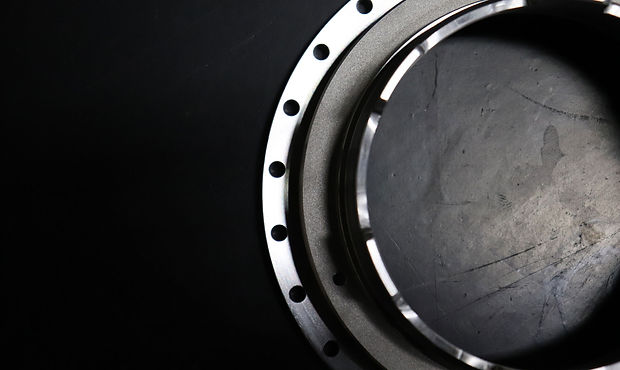
GRIT BLASTING
-
Grit blasting is a surface treatment aimed to modify the surface finish, remove contaminants or give it a certain shape.
-
The surface (usually metal) is modified by propelling media of a certain size and material at a specific velocity (high pressure).
-
Media (abrasive material) used is generally metallic “grit” that range from aluminum, copper and steel. This media is usually crushed, with no specific shape or form.
-
Most common grit sizes offered are:

GLASS BEADING
-
Glass beading is a surface treatment aimed to clean surface areas by applying fine glass beads at a pressure high enough to clean the area treated but low enough not to damage or modify it.
-
The glass beading process is particularly useful to clean thread connections or any other areas that may require other secondary process.
-
Application is very similar to grit blasting, but the media used consist of very small glass beads (silicon) specially manufactured for the glass beading process.
-
Media size depends on the work to be done but generally falls between 30 (0.023”) and 70 (0.008”) mesh.

RUST INHIBITORS
-
Newbec uses Anticorit™, which is a greasy-waxy film rust inhibitor applied to parts or components to prevent corrosion during storage or transportation.
-
It can be applied by dipping, brushing or spraying.
-
Depending on the product used, Anticorit™ can act as a rush inhibitor for 1, 2 or 3 years.
-
Applying Anticorit™ to parts and components has proven to effectively reduce cost of repairing or re-machining them if exposed to corrosive environment conditions.
*Note: Anticorit is a trademark of Fuchs Petrolub SE
SECONDARY PROCESSES
IN PARTNERSHIP
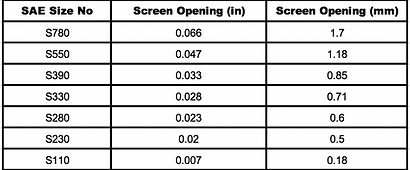
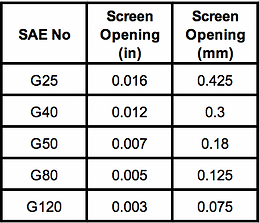
XYLAN COATING
-
Xylan is a dry-film fluoropolymer material with very good lubricant characteristics (low friction) that can operate at very high temperatures and is highly resistant to chemicals.
-
Xylan can be applied as a liquid spray or as a powder.
-
The main application for Xylan is to prevent corrosion and increase product life and it is very good for non-stick applications. For this reason, Xylan can be used on connections or in components under high compressive forces to prevent galling and seizing.
-
Depending on the type of Xylan used, it can display the characteristics shown in the chart on the right.
METALLIC ALLOY COATING
-
Metallic Alloy Coating (MAC) is a process that consists of low porosity-high strength deposits that provide very good wear resistance for high abrasion and erosion environments.
-
It can be applied under relative low temperatures (~ 93°C / 200°F) which makes it ideal for applications where parts cannot be exposed to high heat conditions in order to avoid material changes.
-
MAC can be applied in coat thickness up to 0.015.”
-
Some of the characteristics and benefits of MAC are:
-
Good bond strength (19K – 60K)
-
Hardness 485 – 2600 HV
-
Outstanding corrosion and erosion resistance
-
No ID or OD restrictions
-
Good surface finish w/o polishing after application
-
Excellent sliding wear properties
-
Excellent chemical resistance
-
COPPER PLATING
-
Copper plating is the process by which a layer of copper is electrolytically deposited on the surface of a part or material.
-
The objectives of copper plating are diverse and go from just decorative to highly technical. Copper plating can be used to reduce friction, improve wearability, enhance conductivity and as a corrosion inhibitor, among other things.
NITRIDING
-
Nitriding is a surface treatment aimed to increase hardness, wear and corrosion resistance, and improve fatigue life of the components treated. Additionally, it acts as an anti-galling treatment.
-
The principle behind nitriding is to place the metal (usually carbon steel) in an environment to give up nitrogen under medium heat (around 1000°F); this allows for nitrogen to be diffused into the area of the metal creating a case-hardened surface. It is, therefore, considered a heat-treating process.
-
The thin case-hardened layer varies depending on the process used and can be as thin as 0.002” and as thick as 0.030.” The main two processes used are gas and liquid nitriding.
-
One outstanding feature of nitriding is that it does not affect the core properties of the metal being treated; provided that the nitriding temperature is lower than the tempering temperature of the metal.
HVOF
-
HVOF = High Velocity Oxygen Fuel and is a thermal spray coating process used to increase wear, erosion, abrasion and corrosion resistance, and achieve higher hardness. It can also serve as a seal surface, as long as the process involved does not allow for porosity conditions leading to leakage.
-
The principle behind HVOF is to apply hard particles at supersonic velocity at a controlled high temperature (to a molten or semi-molten state) to achieve high bonding strength.
-
The main purpose of HVOF is to extend the life of the parts or components being treated.
-
HVOF coating thickness varies depending on the material and process used. For most downhole tools, a typical coat thickness varies between 0.001” and 0.020.”
PTA
-
PTA = Plasma Transferred Arc. It is a welding process that allows building a hardface layer on a metal surface.
-
The principle behind PTA is to melt particles by a plasma jet at supersonic speed, atomizing them and propelling the molten particles into a surface.
-
The application of PTA is aimed to highly improve wear, erosion or corrosion resistance.
-
PTA coat thickness varies depending on the material and the application used. For downhole tool applications it is quite common to see thickness between 0.060” and 0.150” with an HV harness also varying between 1400 and 2400.
